How is the CG of rocket found after the complete assembly
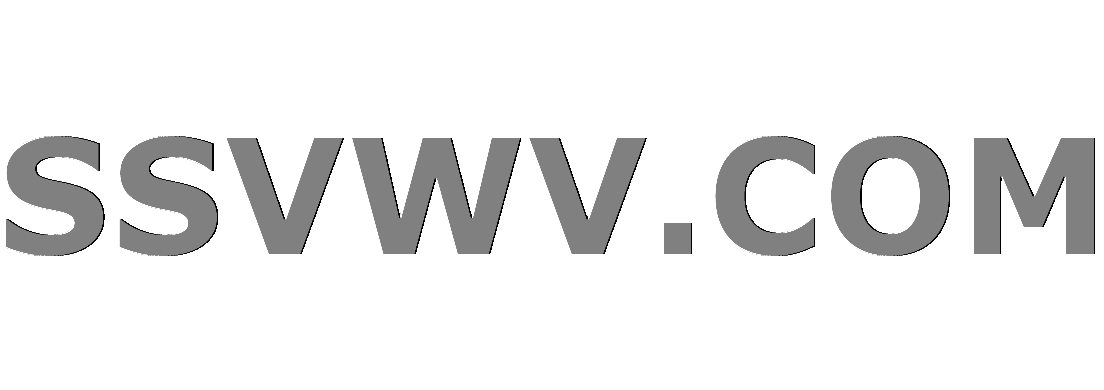
Multi tool use
up vote
8
down vote
favorite
Using CAD modeling, the center of gravity of a rocket can be easily predicted. But in reality, after the assembly, the CG will not be exactly at the place given by the model because of difference in manufacturing of components and other assemblies like plumbing and wiring etc.
So, how is CG determined after complete assembly of the rocket?
rockets center-of-gravity
add a comment |
up vote
8
down vote
favorite
Using CAD modeling, the center of gravity of a rocket can be easily predicted. But in reality, after the assembly, the CG will not be exactly at the place given by the model because of difference in manufacturing of components and other assemblies like plumbing and wiring etc.
So, how is CG determined after complete assembly of the rocket?
rockets center-of-gravity
6
for launch vehicles, knowing the exact CoG isn't necessary -- the software compensates for the behaviour of the vehicle, not the cause.
– JCRM
Nov 29 at 19:55
3
If a very strict quality control is used during manufacture, every part and every subassembley is weighted at different steps of manufacture. If actual weight is different to planned weight, reject the part until the reason for weight difference is found and resolved. You don't want a rocket with substantial differences in structural weight.
– Uwe
Nov 29 at 22:33
4
@JCRM indeed the the CoG varies massively during launch! Liquid fuelled rockets generally have the O2 tank forward of the fuel tank to get the CoG as far forward as possible and so enhance the effect of gimballing the engines. But when the fuel is spent, the CoG moves back. Not to mention the effects of propellant slosh...
– Level River St
Nov 29 at 23:26
add a comment |
up vote
8
down vote
favorite
up vote
8
down vote
favorite
Using CAD modeling, the center of gravity of a rocket can be easily predicted. But in reality, after the assembly, the CG will not be exactly at the place given by the model because of difference in manufacturing of components and other assemblies like plumbing and wiring etc.
So, how is CG determined after complete assembly of the rocket?
rockets center-of-gravity
Using CAD modeling, the center of gravity of a rocket can be easily predicted. But in reality, after the assembly, the CG will not be exactly at the place given by the model because of difference in manufacturing of components and other assemblies like plumbing and wiring etc.
So, how is CG determined after complete assembly of the rocket?
rockets center-of-gravity
rockets center-of-gravity
edited Nov 29 at 22:19


uhoh
33.4k16114410
33.4k16114410
asked Nov 29 at 19:00
Amar
1,009527
1,009527
6
for launch vehicles, knowing the exact CoG isn't necessary -- the software compensates for the behaviour of the vehicle, not the cause.
– JCRM
Nov 29 at 19:55
3
If a very strict quality control is used during manufacture, every part and every subassembley is weighted at different steps of manufacture. If actual weight is different to planned weight, reject the part until the reason for weight difference is found and resolved. You don't want a rocket with substantial differences in structural weight.
– Uwe
Nov 29 at 22:33
4
@JCRM indeed the the CoG varies massively during launch! Liquid fuelled rockets generally have the O2 tank forward of the fuel tank to get the CoG as far forward as possible and so enhance the effect of gimballing the engines. But when the fuel is spent, the CoG moves back. Not to mention the effects of propellant slosh...
– Level River St
Nov 29 at 23:26
add a comment |
6
for launch vehicles, knowing the exact CoG isn't necessary -- the software compensates for the behaviour of the vehicle, not the cause.
– JCRM
Nov 29 at 19:55
3
If a very strict quality control is used during manufacture, every part and every subassembley is weighted at different steps of manufacture. If actual weight is different to planned weight, reject the part until the reason for weight difference is found and resolved. You don't want a rocket with substantial differences in structural weight.
– Uwe
Nov 29 at 22:33
4
@JCRM indeed the the CoG varies massively during launch! Liquid fuelled rockets generally have the O2 tank forward of the fuel tank to get the CoG as far forward as possible and so enhance the effect of gimballing the engines. But when the fuel is spent, the CoG moves back. Not to mention the effects of propellant slosh...
– Level River St
Nov 29 at 23:26
6
6
for launch vehicles, knowing the exact CoG isn't necessary -- the software compensates for the behaviour of the vehicle, not the cause.
– JCRM
Nov 29 at 19:55
for launch vehicles, knowing the exact CoG isn't necessary -- the software compensates for the behaviour of the vehicle, not the cause.
– JCRM
Nov 29 at 19:55
3
3
If a very strict quality control is used during manufacture, every part and every subassembley is weighted at different steps of manufacture. If actual weight is different to planned weight, reject the part until the reason for weight difference is found and resolved. You don't want a rocket with substantial differences in structural weight.
– Uwe
Nov 29 at 22:33
If a very strict quality control is used during manufacture, every part and every subassembley is weighted at different steps of manufacture. If actual weight is different to planned weight, reject the part until the reason for weight difference is found and resolved. You don't want a rocket with substantial differences in structural weight.
– Uwe
Nov 29 at 22:33
4
4
@JCRM indeed the the CoG varies massively during launch! Liquid fuelled rockets generally have the O2 tank forward of the fuel tank to get the CoG as far forward as possible and so enhance the effect of gimballing the engines. But when the fuel is spent, the CoG moves back. Not to mention the effects of propellant slosh...
– Level River St
Nov 29 at 23:26
@JCRM indeed the the CoG varies massively during launch! Liquid fuelled rockets generally have the O2 tank forward of the fuel tank to get the CoG as far forward as possible and so enhance the effect of gimballing the engines. But when the fuel is spent, the CoG moves back. Not to mention the effects of propellant slosh...
– Level River St
Nov 29 at 23:26
add a comment |
3 Answers
3
active
oldest
votes
up vote
14
down vote
Modern CAD software is very good and can include the mass of every zip tie and weld if it's made with enough care. If the real life doesn't match up with plans, the whole rocket can be put on multiple load sensors and from that the CG can be calculated. However, finding the CG is still important, especially in flight when mass is changing due to fuel consumption and rocket staging.
When an object is in flight or is not constrained, it rotates about its CG. This means if you spread accelerometers around the object and compare the different readings of those sensors, the CG can be calculated quickly. For more detail on this technique, you can read this paper: https://www.mdpi.com/1424-8220/14/9/17567/htm
add a comment |
up vote
7
down vote
For the Apollo program, there was a device that measured the weight and balance of the completed modules. Page 9-4 of the Apollo Program Summary Report describes the steps in manufacturing the Command Module:
9.1.1.3 Final operations: In the final phase of command module manufacturing, the vehicle was cycled through another tumble-and-clean operation in which the vehicle was rotated through 360° in each axis to dislodge and remove debris. The weight and center of gravity were then determined, and the vehicle was subjected to an integrated test (sec. 9.1.5). The command module was subsequently moved to the shipping area and prepared for shipment. Such items as crew couches and crew equipment were removed, packed, and shipped separately.
The manufacturing of the Service Module is described on page 9-6:
Following the tests, the vehicle was cycled through the tumble-and-clean positioner to dislodge and remove debris. The cleaned vehicle was then weighed and its center of gravity determined. On completion of these operations, the vehicle was placed in the integrated test stand for the integrated test series described in section 9.1.5. The integrated test completed the manufacturing, test, and checkout operations, and the vehicle was mounted on a shipping pallet and prepared for shipment.
Both operations were performed on a piece of equipment called the "weight and balance fixture":
add a comment |
up vote
0
down vote
The exact CG position is (never?) required
You just need a good CAD approximation (and maybe verifying the CG of complicated heavy parts if strong doubts still exist). Then you qualify your GNC algorithms taking into account all the variations you can predict (and some marging for the ones you cannot).
When accelerometers are used, for example on Ariane, it is to measure the dynamic state of the launcher, i.e. which dynamic structural mode is active, to avoid control errors (and amplifying dynamic mode)
New contributor
Olivier is a new contributor to this site. Take care in asking for clarification, commenting, and answering.
Check out our Code of Conduct.
add a comment |
3 Answers
3
active
oldest
votes
3 Answers
3
active
oldest
votes
active
oldest
votes
active
oldest
votes
up vote
14
down vote
Modern CAD software is very good and can include the mass of every zip tie and weld if it's made with enough care. If the real life doesn't match up with plans, the whole rocket can be put on multiple load sensors and from that the CG can be calculated. However, finding the CG is still important, especially in flight when mass is changing due to fuel consumption and rocket staging.
When an object is in flight or is not constrained, it rotates about its CG. This means if you spread accelerometers around the object and compare the different readings of those sensors, the CG can be calculated quickly. For more detail on this technique, you can read this paper: https://www.mdpi.com/1424-8220/14/9/17567/htm
add a comment |
up vote
14
down vote
Modern CAD software is very good and can include the mass of every zip tie and weld if it's made with enough care. If the real life doesn't match up with plans, the whole rocket can be put on multiple load sensors and from that the CG can be calculated. However, finding the CG is still important, especially in flight when mass is changing due to fuel consumption and rocket staging.
When an object is in flight or is not constrained, it rotates about its CG. This means if you spread accelerometers around the object and compare the different readings of those sensors, the CG can be calculated quickly. For more detail on this technique, you can read this paper: https://www.mdpi.com/1424-8220/14/9/17567/htm
add a comment |
up vote
14
down vote
up vote
14
down vote
Modern CAD software is very good and can include the mass of every zip tie and weld if it's made with enough care. If the real life doesn't match up with plans, the whole rocket can be put on multiple load sensors and from that the CG can be calculated. However, finding the CG is still important, especially in flight when mass is changing due to fuel consumption and rocket staging.
When an object is in flight or is not constrained, it rotates about its CG. This means if you spread accelerometers around the object and compare the different readings of those sensors, the CG can be calculated quickly. For more detail on this technique, you can read this paper: https://www.mdpi.com/1424-8220/14/9/17567/htm
Modern CAD software is very good and can include the mass of every zip tie and weld if it's made with enough care. If the real life doesn't match up with plans, the whole rocket can be put on multiple load sensors and from that the CG can be calculated. However, finding the CG is still important, especially in flight when mass is changing due to fuel consumption and rocket staging.
When an object is in flight or is not constrained, it rotates about its CG. This means if you spread accelerometers around the object and compare the different readings of those sensors, the CG can be calculated quickly. For more detail on this technique, you can read this paper: https://www.mdpi.com/1424-8220/14/9/17567/htm
edited Nov 29 at 21:26
answered Nov 29 at 19:31


Dragongeek
3,2671330
3,2671330
add a comment |
add a comment |
up vote
7
down vote
For the Apollo program, there was a device that measured the weight and balance of the completed modules. Page 9-4 of the Apollo Program Summary Report describes the steps in manufacturing the Command Module:
9.1.1.3 Final operations: In the final phase of command module manufacturing, the vehicle was cycled through another tumble-and-clean operation in which the vehicle was rotated through 360° in each axis to dislodge and remove debris. The weight and center of gravity were then determined, and the vehicle was subjected to an integrated test (sec. 9.1.5). The command module was subsequently moved to the shipping area and prepared for shipment. Such items as crew couches and crew equipment were removed, packed, and shipped separately.
The manufacturing of the Service Module is described on page 9-6:
Following the tests, the vehicle was cycled through the tumble-and-clean positioner to dislodge and remove debris. The cleaned vehicle was then weighed and its center of gravity determined. On completion of these operations, the vehicle was placed in the integrated test stand for the integrated test series described in section 9.1.5. The integrated test completed the manufacturing, test, and checkout operations, and the vehicle was mounted on a shipping pallet and prepared for shipment.
Both operations were performed on a piece of equipment called the "weight and balance fixture":
add a comment |
up vote
7
down vote
For the Apollo program, there was a device that measured the weight and balance of the completed modules. Page 9-4 of the Apollo Program Summary Report describes the steps in manufacturing the Command Module:
9.1.1.3 Final operations: In the final phase of command module manufacturing, the vehicle was cycled through another tumble-and-clean operation in which the vehicle was rotated through 360° in each axis to dislodge and remove debris. The weight and center of gravity were then determined, and the vehicle was subjected to an integrated test (sec. 9.1.5). The command module was subsequently moved to the shipping area and prepared for shipment. Such items as crew couches and crew equipment were removed, packed, and shipped separately.
The manufacturing of the Service Module is described on page 9-6:
Following the tests, the vehicle was cycled through the tumble-and-clean positioner to dislodge and remove debris. The cleaned vehicle was then weighed and its center of gravity determined. On completion of these operations, the vehicle was placed in the integrated test stand for the integrated test series described in section 9.1.5. The integrated test completed the manufacturing, test, and checkout operations, and the vehicle was mounted on a shipping pallet and prepared for shipment.
Both operations were performed on a piece of equipment called the "weight and balance fixture":
add a comment |
up vote
7
down vote
up vote
7
down vote
For the Apollo program, there was a device that measured the weight and balance of the completed modules. Page 9-4 of the Apollo Program Summary Report describes the steps in manufacturing the Command Module:
9.1.1.3 Final operations: In the final phase of command module manufacturing, the vehicle was cycled through another tumble-and-clean operation in which the vehicle was rotated through 360° in each axis to dislodge and remove debris. The weight and center of gravity were then determined, and the vehicle was subjected to an integrated test (sec. 9.1.5). The command module was subsequently moved to the shipping area and prepared for shipment. Such items as crew couches and crew equipment were removed, packed, and shipped separately.
The manufacturing of the Service Module is described on page 9-6:
Following the tests, the vehicle was cycled through the tumble-and-clean positioner to dislodge and remove debris. The cleaned vehicle was then weighed and its center of gravity determined. On completion of these operations, the vehicle was placed in the integrated test stand for the integrated test series described in section 9.1.5. The integrated test completed the manufacturing, test, and checkout operations, and the vehicle was mounted on a shipping pallet and prepared for shipment.
Both operations were performed on a piece of equipment called the "weight and balance fixture":
For the Apollo program, there was a device that measured the weight and balance of the completed modules. Page 9-4 of the Apollo Program Summary Report describes the steps in manufacturing the Command Module:
9.1.1.3 Final operations: In the final phase of command module manufacturing, the vehicle was cycled through another tumble-and-clean operation in which the vehicle was rotated through 360° in each axis to dislodge and remove debris. The weight and center of gravity were then determined, and the vehicle was subjected to an integrated test (sec. 9.1.5). The command module was subsequently moved to the shipping area and prepared for shipment. Such items as crew couches and crew equipment were removed, packed, and shipped separately.
The manufacturing of the Service Module is described on page 9-6:
Following the tests, the vehicle was cycled through the tumble-and-clean positioner to dislodge and remove debris. The cleaned vehicle was then weighed and its center of gravity determined. On completion of these operations, the vehicle was placed in the integrated test stand for the integrated test series described in section 9.1.5. The integrated test completed the manufacturing, test, and checkout operations, and the vehicle was mounted on a shipping pallet and prepared for shipment.
Both operations were performed on a piece of equipment called the "weight and balance fixture":
answered Nov 29 at 21:31
Dr Sheldon
4,1781344
4,1781344
add a comment |
add a comment |
up vote
0
down vote
The exact CG position is (never?) required
You just need a good CAD approximation (and maybe verifying the CG of complicated heavy parts if strong doubts still exist). Then you qualify your GNC algorithms taking into account all the variations you can predict (and some marging for the ones you cannot).
When accelerometers are used, for example on Ariane, it is to measure the dynamic state of the launcher, i.e. which dynamic structural mode is active, to avoid control errors (and amplifying dynamic mode)
New contributor
Olivier is a new contributor to this site. Take care in asking for clarification, commenting, and answering.
Check out our Code of Conduct.
add a comment |
up vote
0
down vote
The exact CG position is (never?) required
You just need a good CAD approximation (and maybe verifying the CG of complicated heavy parts if strong doubts still exist). Then you qualify your GNC algorithms taking into account all the variations you can predict (and some marging for the ones you cannot).
When accelerometers are used, for example on Ariane, it is to measure the dynamic state of the launcher, i.e. which dynamic structural mode is active, to avoid control errors (and amplifying dynamic mode)
New contributor
Olivier is a new contributor to this site. Take care in asking for clarification, commenting, and answering.
Check out our Code of Conduct.
add a comment |
up vote
0
down vote
up vote
0
down vote
The exact CG position is (never?) required
You just need a good CAD approximation (and maybe verifying the CG of complicated heavy parts if strong doubts still exist). Then you qualify your GNC algorithms taking into account all the variations you can predict (and some marging for the ones you cannot).
When accelerometers are used, for example on Ariane, it is to measure the dynamic state of the launcher, i.e. which dynamic structural mode is active, to avoid control errors (and amplifying dynamic mode)
New contributor
Olivier is a new contributor to this site. Take care in asking for clarification, commenting, and answering.
Check out our Code of Conduct.
The exact CG position is (never?) required
You just need a good CAD approximation (and maybe verifying the CG of complicated heavy parts if strong doubts still exist). Then you qualify your GNC algorithms taking into account all the variations you can predict (and some marging for the ones you cannot).
When accelerometers are used, for example on Ariane, it is to measure the dynamic state of the launcher, i.e. which dynamic structural mode is active, to avoid control errors (and amplifying dynamic mode)
New contributor
Olivier is a new contributor to this site. Take care in asking for clarification, commenting, and answering.
Check out our Code of Conduct.
New contributor
Olivier is a new contributor to this site. Take care in asking for clarification, commenting, and answering.
Check out our Code of Conduct.
answered 2 days ago
Olivier
1012
1012
New contributor
Olivier is a new contributor to this site. Take care in asking for clarification, commenting, and answering.
Check out our Code of Conduct.
New contributor
Olivier is a new contributor to this site. Take care in asking for clarification, commenting, and answering.
Check out our Code of Conduct.
Olivier is a new contributor to this site. Take care in asking for clarification, commenting, and answering.
Check out our Code of Conduct.
add a comment |
add a comment |
Thanks for contributing an answer to Space Exploration Stack Exchange!
- Please be sure to answer the question. Provide details and share your research!
But avoid …
- Asking for help, clarification, or responding to other answers.
- Making statements based on opinion; back them up with references or personal experience.
Use MathJax to format equations. MathJax reference.
To learn more, see our tips on writing great answers.
Some of your past answers have not been well-received, and you're in danger of being blocked from answering.
Please pay close attention to the following guidance:
- Please be sure to answer the question. Provide details and share your research!
But avoid …
- Asking for help, clarification, or responding to other answers.
- Making statements based on opinion; back them up with references or personal experience.
To learn more, see our tips on writing great answers.
Sign up or log in
StackExchange.ready(function () {
StackExchange.helpers.onClickDraftSave('#login-link');
});
Sign up using Google
Sign up using Facebook
Sign up using Email and Password
Post as a guest
Required, but never shown
StackExchange.ready(
function () {
StackExchange.openid.initPostLogin('.new-post-login', 'https%3a%2f%2fspace.stackexchange.com%2fquestions%2f32426%2fhow-is-the-cg-of-rocket-found-after-the-complete-assembly%23new-answer', 'question_page');
}
);
Post as a guest
Required, but never shown
Sign up or log in
StackExchange.ready(function () {
StackExchange.helpers.onClickDraftSave('#login-link');
});
Sign up using Google
Sign up using Facebook
Sign up using Email and Password
Post as a guest
Required, but never shown
Sign up or log in
StackExchange.ready(function () {
StackExchange.helpers.onClickDraftSave('#login-link');
});
Sign up using Google
Sign up using Facebook
Sign up using Email and Password
Post as a guest
Required, but never shown
Sign up or log in
StackExchange.ready(function () {
StackExchange.helpers.onClickDraftSave('#login-link');
});
Sign up using Google
Sign up using Facebook
Sign up using Email and Password
Sign up using Google
Sign up using Facebook
Sign up using Email and Password
Post as a guest
Required, but never shown
Required, but never shown
Required, but never shown
Required, but never shown
Required, but never shown
Required, but never shown
Required, but never shown
Required, but never shown
Required, but never shown
aJXDCB9o0j,oyphP,2FhVwBSkwWy,lJiWUQ5BCbt7dHWWhUxQYCs1iYRPXd,M ngH,ZatcWXwM
6
for launch vehicles, knowing the exact CoG isn't necessary -- the software compensates for the behaviour of the vehicle, not the cause.
– JCRM
Nov 29 at 19:55
3
If a very strict quality control is used during manufacture, every part and every subassembley is weighted at different steps of manufacture. If actual weight is different to planned weight, reject the part until the reason for weight difference is found and resolved. You don't want a rocket with substantial differences in structural weight.
– Uwe
Nov 29 at 22:33
4
@JCRM indeed the the CoG varies massively during launch! Liquid fuelled rockets generally have the O2 tank forward of the fuel tank to get the CoG as far forward as possible and so enhance the effect of gimballing the engines. But when the fuel is spent, the CoG moves back. Not to mention the effects of propellant slosh...
– Level River St
Nov 29 at 23:26